在汽车工业中,有限元分析(FEA)已成为设计、验证和优化的核心工具,覆盖从整车性能到零部件细节的全流程开发。以下是其在汽车领域的关键应用及典型案例:
1. 车身结构与轻量化设计(如图1)
应用场景:车身刚度分析、材料替代(如钢→铝/碳纤维)、拓扑优化(减重同时满足碰撞标准)。
关键指标:静态扭转刚度(目标通常>20 kN·m/°)、模态频率(避免与路面激励共振,如轿车一阶模态>30Hz)。
2. 碰撞安全与乘员保护(如图2)
法规要求:满足NCAP、FMVSS等标准(如正面碰撞56km/h、侧碰50km/h)。
FEA作用:模拟气囊展开时序、安全带载荷传递、B柱侵入量(目标<150mm)。
3. 底盘与悬挂系统耐久性(如图3)
分析类型:多体动力学(MBD)与FEA联合仿真,预测控制臂、转向节等部件的疲劳寿命。
载荷输入:基于实测路谱(如比利时路况)或虚拟路面(ISO 8608标准)。
4. 动力总成NVH优化(如图4)
问题场景:发动机振动传递至车厢(如怠速抖动<0.3m/s²)、齿轮啸叫噪声。
方法:模态叠加法分析结构传递路径,优化支架刚度或添加阻尼材料。
5. 电池包结构与热管理(新能源车 如图5)
机械安全:模拟电池箱体在挤压/跌落工况下的变形(如国标GB 38031要求30分钟内无起火)。
热失控仿真:电芯热滥用(>150℃)时的热蔓延预测,优化冷却板设计。
6. 空气动力学与流体-结构耦合(如图6)
应用:外流场减阻(风阻系数目标<0.3)、雨刮/后视镜风噪分析。
工具链:Star-CCM+或Fluent耦合FEA分析柔性部件(如天窗颤振)。
7. 智能制造与工艺仿真(如图7)
冲压成型:预测钣金件回弹量(补偿模具设计,精度<0.1mm)。
焊接变形:白车身焊装序列优化(采用一体压铸后焊点减少70%)。
典型软件工具
碰撞/安全:LS-DYNA、PAM-CRASH
疲劳分析:nCode、FE-SAFE
多物理场:ANSYS Workbench、COMSOL
优化设计:OptiStruct、HEEDS
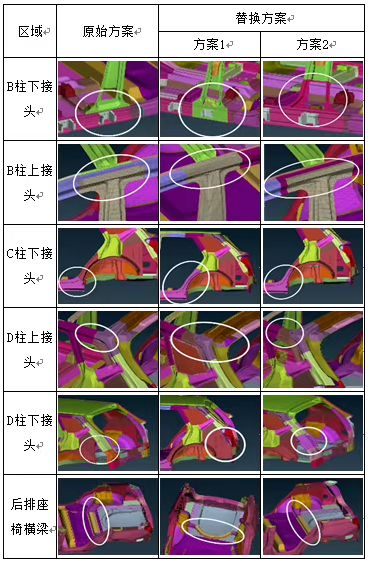
图1 车身关键部位结构优化方案
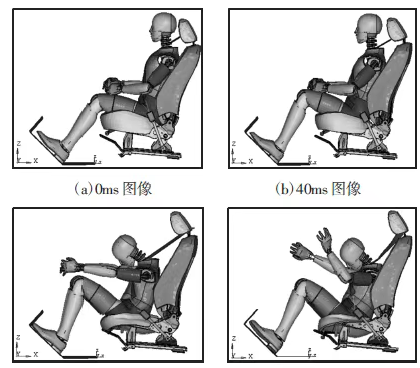
图2 前排座椅正面碰撞过程图
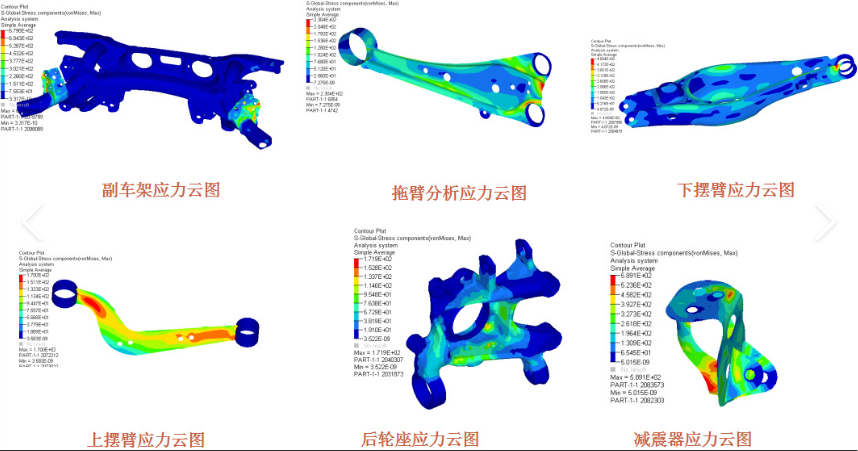
图3 汽车底盘关键零件应力云图
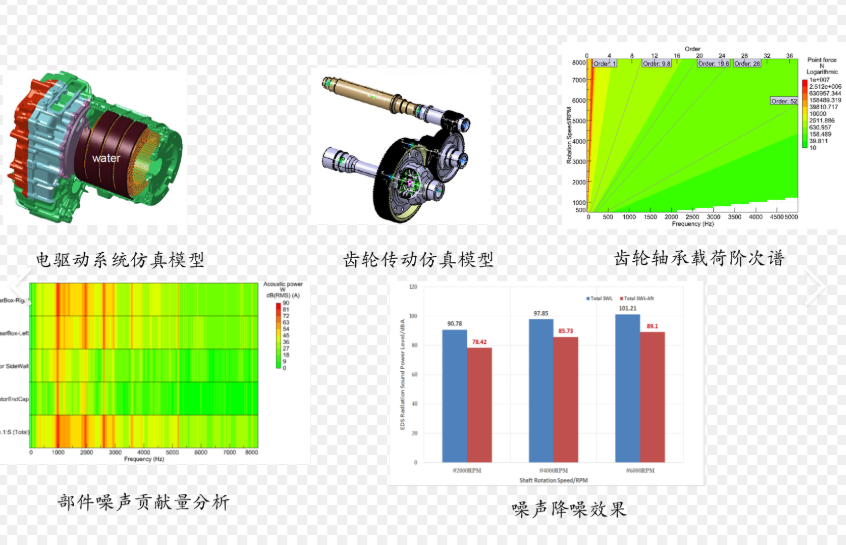
图4 动力总成NVH优化
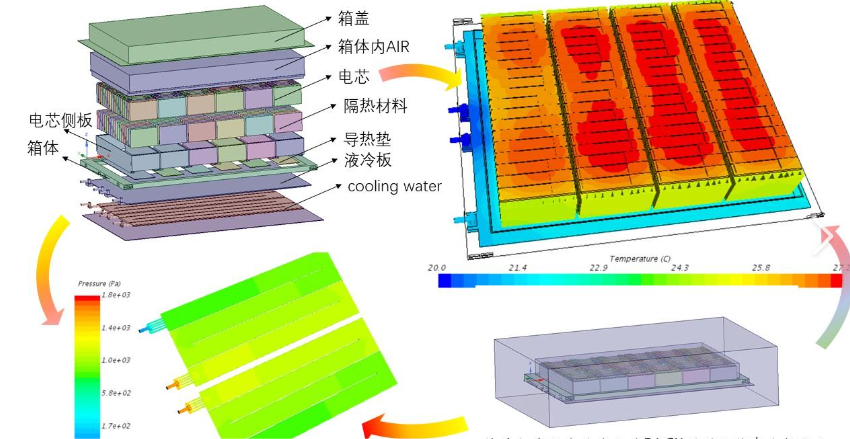
图5 电池包结构与热管理
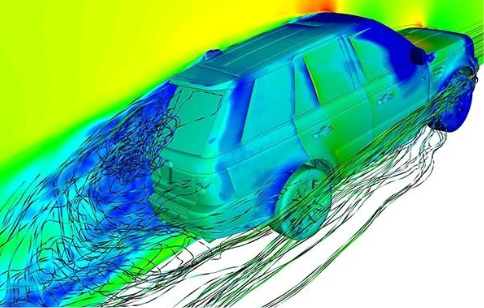
图6 汽车空气动力学仿真分析
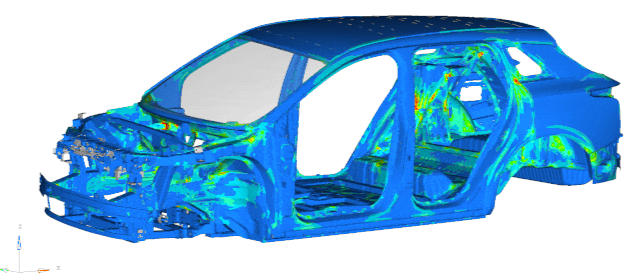
图7 一体压铸仿真结果图